
We had a great time hosting a Cabinet Makers Association shop tour at Dark Horse just ahead of the International Woodworkers Fair in Atlanta in August.
Dark Horse was the final stop on a three-shop tour – the August 21 tour also included two other Atlanta-area shops, Atlanta Cabinet Shop and Custom Creative Furniture.
Give and take
We were able to show our 50 guests – fellow CMA members from all over the country – our set-up and the technology we use, and answer questions about how we operate.
And as I’d hoped, we also got some feedback and ideas about how we could improve our way of doing things. The ideas ranged from workflow suggestions to little tweaks we could make to save steps (and therefore time) – for instance, shifting the location of an assembly table.
We knew our lighting wasn’t great, but we didn’t realize how bad it was until getting several questions and comments about it; we’ve already added some additional lighting and plan to add more.
The most surprising question during the tour? “Hey, since you don’t use that [fill in the blank] much, can I buy it from you?” It’s pretty obvious what equipment we don’t use because it’s all shoved into one area that’s completely inaccessible unless you move other things around. (The answer was always, “Sorry, no.”)
Perks
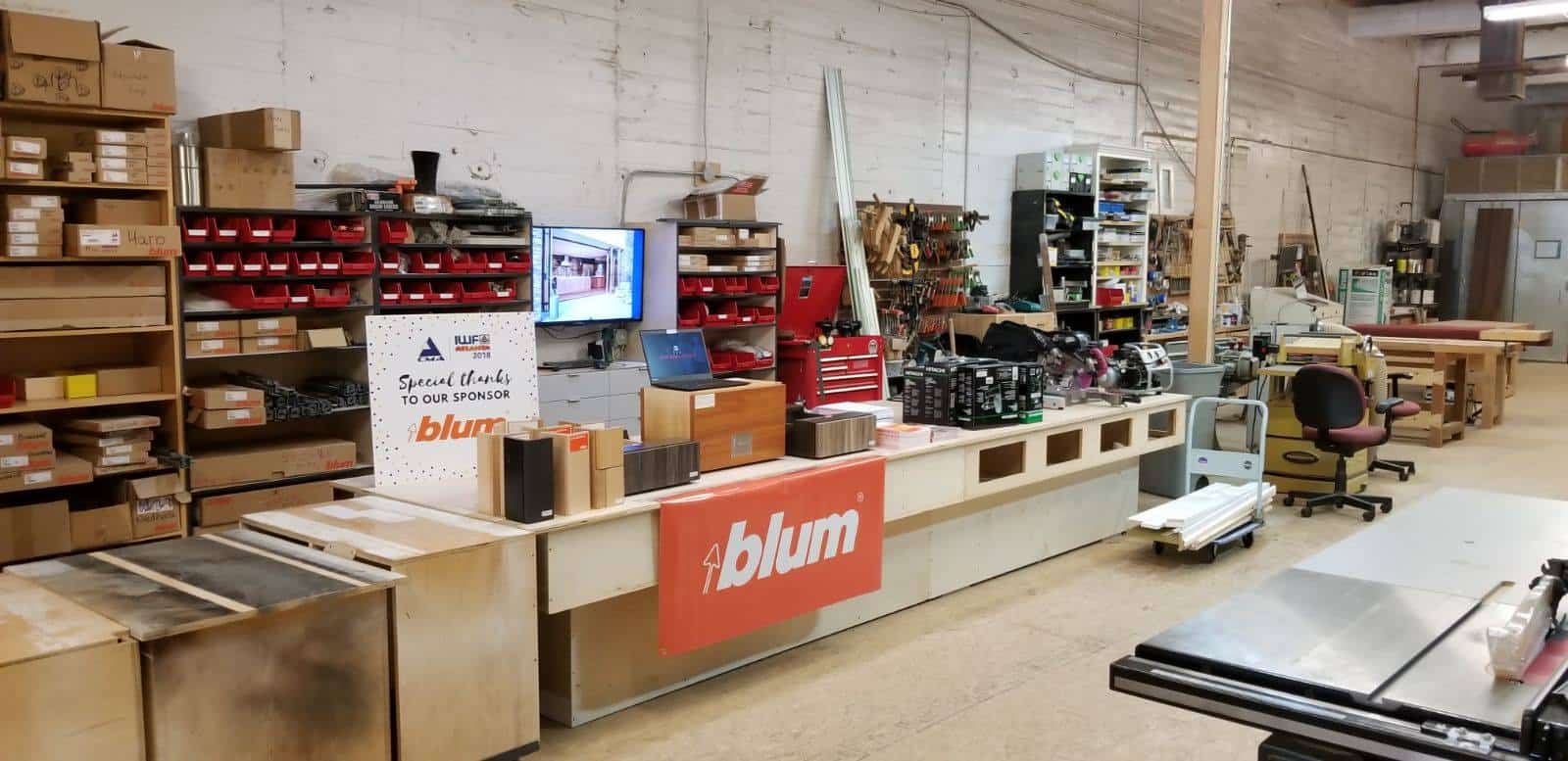
Our tour stop was sponsored by Rugby Architectural Building Products (which distributes plywood, specialty panels, and hardware); Blum (hardware manufacturer); Jones Metal Molding (local company that is a distributor for Blum and other cabinet hardware); and CAMaster, the maker of Dark Horse’s CNC machine.
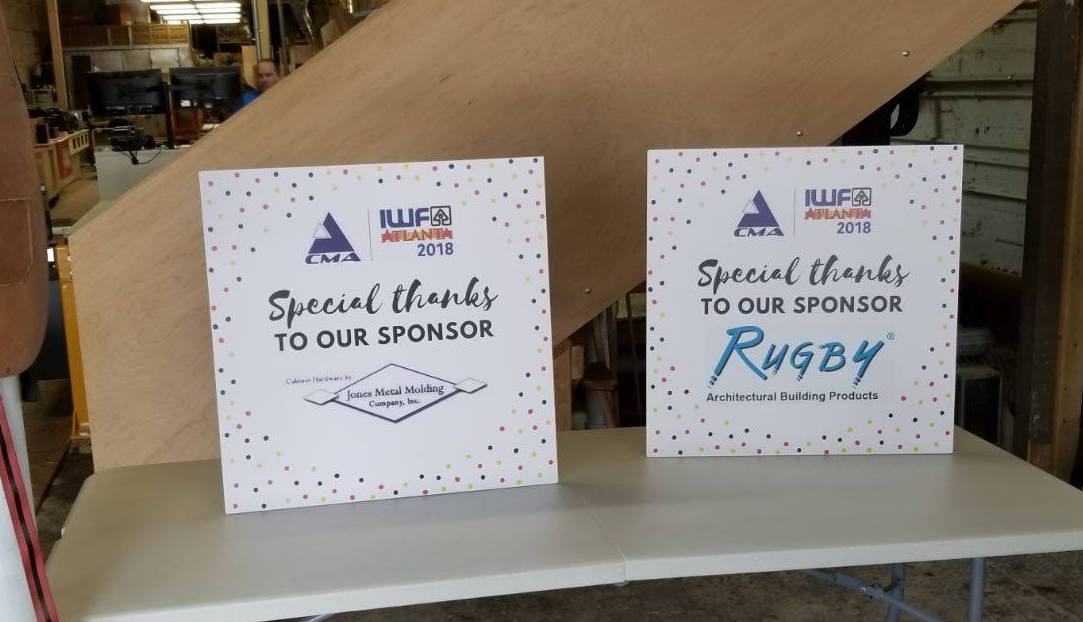
Thanks to Hitachi Koki USA, there was a drawing for a Hitachi power tool, and Hitachi and Blum offered demos.
And to cap off the day, we had some surprise Southern hospitality planned for our guests. Around 4:15, a truck arrived, pulling an already-smoking smoker loaded with food for a post-tour barbecue.
It was truly a feast, and I don’t think it would be bragging (or an exaggeration) to say that a good time was had by all.
Thanks to the CMA for including Dark Horse in such a great event.
~ Chris Dehmer
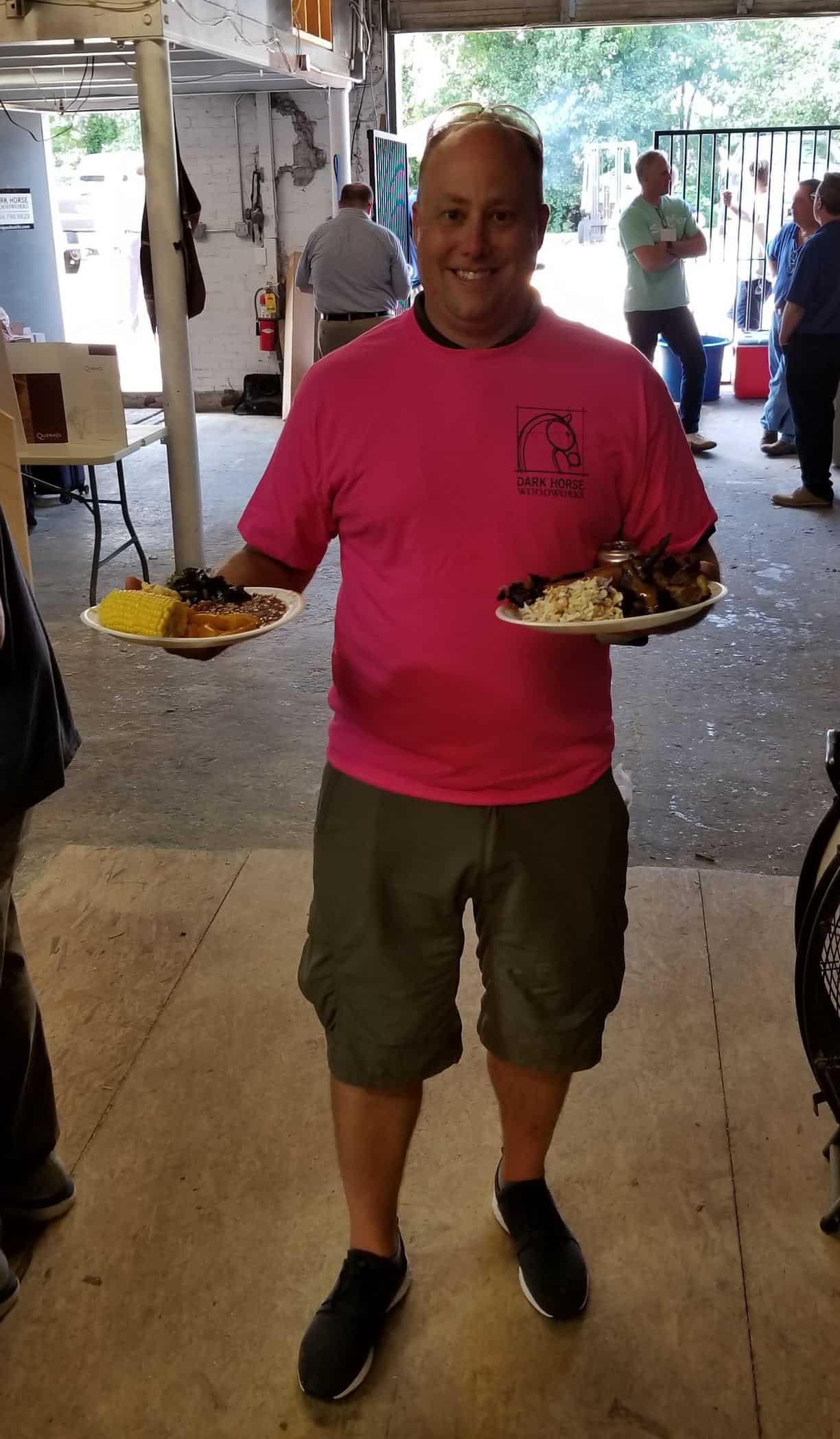